KOMORY WĘDZARNICZO-PARZELNICZE „IWYSOCKI” z uwagi na segmentową budowę składającą się z 1-wózkowych modułów można kompletować w wielo-wózkowe kompakty w zależności od potrzeb klienta. W KOMORACH WĘDZARNICZO-PARZELNICZYCH „IWYSOCKI można stosować różne nośniki energii: produkujemy komory parowe, elektryczne, olejowe, gazowe lub mieszane np. parowo-elektryczne.
Projektując KOMORY WĘDZARNICZO-PARZELNICZE „IWYSOCKI” stosujemy rozwiązania, które stawiają je wśród najlepszych urządzeń na rynku.
Pragniemy zwrócić uwagę na niektóre elementy które je wyróżniają:
- użyte materiały są najwyższej jakości.
- uwzględniamy indywidualne preferencje klienta.
- wzmocniona konstrukcja oraz podłoga przystosowana do bardzo dużych obciążeń.
- wzmocnione poszycie ściany przedniej i drzwi.
- warstwowa konstrukcja ścian i sufitów (ściany i sufity 60mm, drzwi 80mm).
- izolacja ścian, sufitów i drzwi z pianki poliuretanowej.
- technika połączeń zapewniająca szczelność.
- mikroprocesorowy układ sterowania z rejestracją przebiegu procesu.
- komora może współpracować z różnymi generatorami dymu.
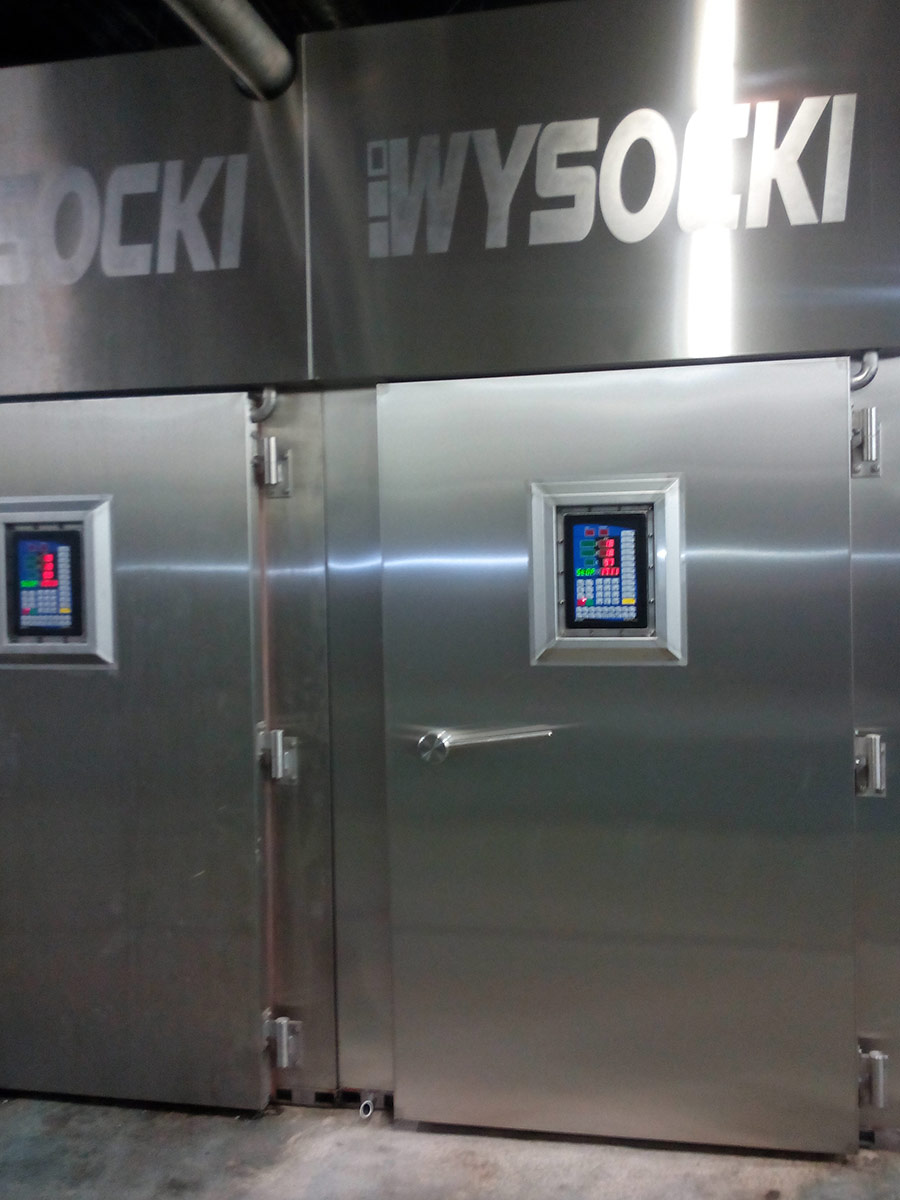
Przeznaczenie
Komora służy do prowadzania procesu obróbki termicznej mięsa, wędlin, ryb, serów i innych produktów.
Współpracuje z dymogeneratorem i opcjonalnie z innymi urządzeniami np. agregat chłodniczy, atomizer płynnego dymu.
Wymiary wózków wędzarniczych 1000x 1000x2000mm.
Podstawowe procesy to: osadzanie, suszenie, wędzenie zimne i gorące, parzenie, gotowanie, barwienie, pieczenie, rozmrażanie i wiele innych procesów technologicznych.
- uzyskiwanie bardzo dobrych wskaźników technologicznych.
- niezawodne prowadzenie procesu technologicznego
- trwała , solidna i szczelna budowa kompaktowa
- pneumatyczny układ sterowania klapami i zaworami
- niskie zapotrzebowanie energetyczne
- niska cena
Układ sterowania
Komora wyposażona jest w niezawodne sterowanie mikroprocesorowe oparte na sterowniku MCC 2100 firmy Mikster, który dedykowany jest do komór wędzarniczo-parzelniczych. Sterownik pozwala wpisać do pamięci wiele indywidualnych programów do obróbki wyrobów. Obsługa ma możliwość bezpośredniego monitorowania takich parametrów jak ; temperatura komory, temperatura wsadu wewnątrz produktu, wilgotność względną powietrza w komorze, temperatura dymu, itp. Sterownik steruje również pracą dymogeneratora, pozwala w sposób precyzyjny prowadzić cykl produkcyjny oraz zmieniać parametry pracy urządzenia.
Układ mycia komory.
Układ Mycia komory jest w pełni zautomatyzowany. Rozprowadzanie czynnika myjącego do poszczególnych punktów komory, rurociągów i dymogeneratora odbywa się kolektorem przebiegającym wzdłuż dachu komory. Na każdym segmencie komory kolektor dzieli się na dwa rozgałęzienia, z których jedno doprowadza czynnik myjący do wentylatora obiegu powietrza a drugie rozgałęzienie doprowadza czynnik myjący do wentylatora wyciągu i dymogeneratora. Czynnik myjący oraz wodę wraz ze sprężonym powietrzem do mycia i płukania komory dozuje pompa SEKO 04. Sterowanie pompą i elektrozaworami przyporządkowane jest programowi “Mycie”.
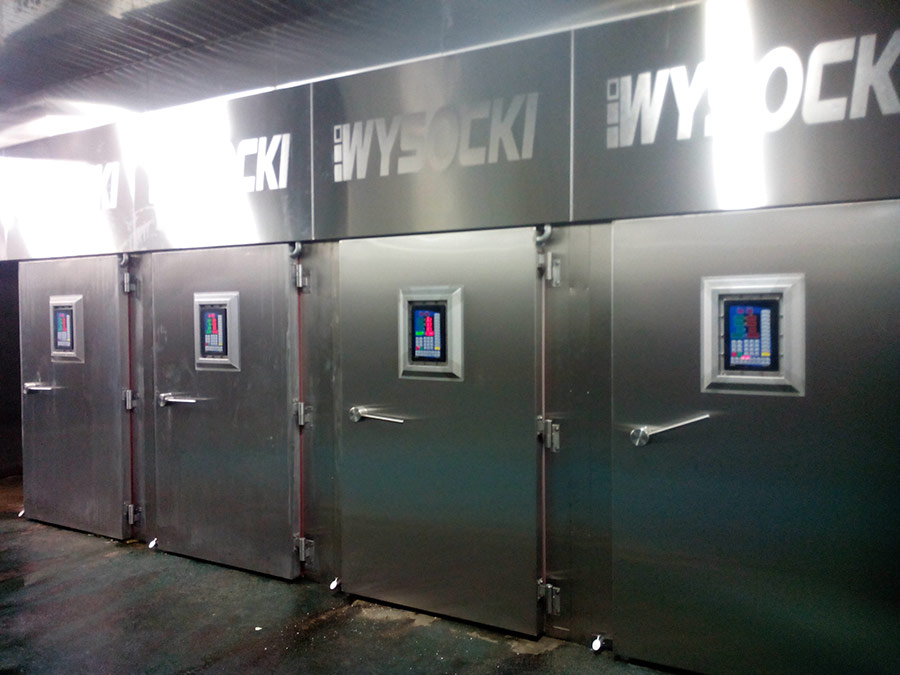
Układ pomiaru temperatury i wilgotności.
Do pomiaru temperatury i wilgotności względnej w komorze służą dwa czujniki typu: Pt100.
Przy pomocy jednego czujnika mierzy się temperaturę “suchą”, przy pomocy drugiego temperaturę “wilgotną”. Czujnik temperatury “mokrej” jest utrzymywany w wilgotności poprzez opaskę zanurzoną w zbiorniczku . Różnica psychometryczna jest analizowana przez mikroprocesor i po przetworzeniu podawana jako procentowa wilgotność względna.
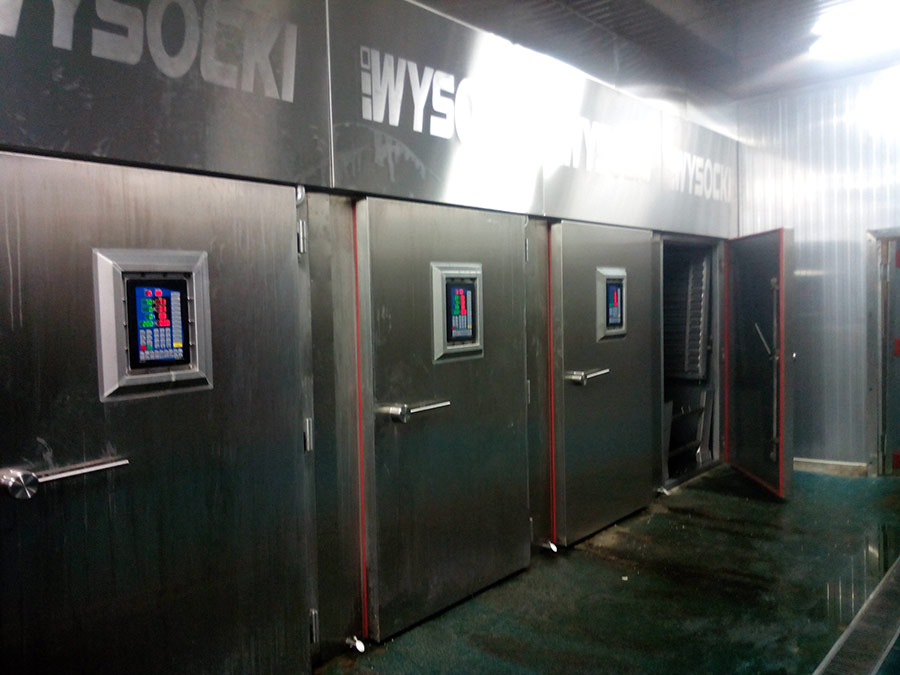
Układ pomiaru temperatury rdzenia batonu.
Do pomiaru temperatury rdzenia batonu zastosowano czujniki typu Pt100. Czujnik o średnicy 6mm jest wykonany ze stali nierdzewnej.
Końcówka czujnika jest zaostrzona w celu łatwego wbicia czujnika do batonu. Czujnik jest umocowany w uchwycie na ścianie przedniej komory.
INNOWACYJNE ROZWIĄZANIA oraz wynikacjace z nich zalety zastosowane w KOMORZE WĘDZARNICZO PARZELNICZEJ „IWYSOCKI”
- Zastosowanie „kierownic” do rozprowadzania świeżego powietrza pozwala na równomierne suszenie produktu góra – dół. Rozwiązanie stosowane jako nowość wśród polskich producentów.
- Innowcyjny sposób rozprowadzenia pary o niskim ciśnieniu i prowadzenie kroku parzenie bez konieczności pracy wentylatorów z zachowaniem równomierności rozkładu temperatur co daje możliwośćograniczenia masy ubytków gotowego wyrobu.
- Wpięcie odprowadzenia dymu z komory do płuczki wodnej przez co komora nie jest uciążliwa dla otoczenia oraz nie wymaga dużych nakładów energetycznych na oczyszczenie spalin.
- Zastosowanie układu mycia z wykorzystaniem pompy dozującej SEKO pozwala spełnić rygorystyczne przepisy BHP nie wymaga rozcieńczanie środków myjących, ponieważ koncentrat zasysany jest przez pompę, mieszany z wodą i powietrzem i dozowany do układu mycia.
- Zastosowano innowacyjne rozwiązanie w budowie dymogeneratora, które pozwala na odcinanie zasobnika wiórków od komory spalania podczas postoju dymogeneratora co pozwala na oszczędności i kontrolowanie procesu spalania wiórków.
- Zastosowanie pianki poliuretanowej do izolacji ścian oraz ograniczenie mostków termicznych powoduje, że straty energetyczne są bardzo niskie.
- Z badań użytkowników naszych komór wynika ,że produkty na nich wytwarzane spełniają najnowsze normy dotyczące zawartości substancji szkodliwych (WWA).